Well all I can say is I am glad I organised the trip as it was well worth it and thanks to the other 15 members who took time out to attend
We started off in the lineage centre where there was a lot about the history of Bentley and a few cars including W O Bentleys own 8 litre , this was the only place pictures were allowed
We then went on to the factory tour and were lucky that the factory was fully operational so we saw lots of different processes most of which are by hand which is something Bentley pride themselves on
We saw the steering wheel stitching section and saw the leather being marked with the prongs of a kitchen fork before the impressions were then made into the holes for stitching with a bradall
The process for making seats start with the hides being inspected for any blemishes , those that are too bad to put in the car are marked in orange and others not quite so bad were marked in white. The white ones will be used in the car but out of sight such as under the seat or glovebox where the customer will never see them , the quality control is amazing as where some of the hides were marked as unsuitable you could hardly see any marks at all.
The hide is then stretched onto a large table where an automated cutter cuts out various sections but is intelligent enough to miss the orange marked sections.
The cut out leather then goes to a section where the sub sections of the seats are assembled before going to final assembly to fit on the frames , the stitching can be in all different colours or even cross stitched and the final product looks stunning
Some of us like our walnut accessories but the wood section at Bentley is something else, we were told how the wood is bought in Spain at a fayre where suppliers from all over the world gather to sell their products and Bentley bid for what they want. The wood is very thinly sliced and cut into oblong sections and stored to get some moisture back into it, it is then pressed and the shape cut with a laser cutter before it is fitted on the various sections of the car , eg glovebox lid, door cappings etc . At this stage it is still rough to the touch so it is sanded before having 5 costs of lacquer applied by machine, , left for 3 days to harden, after which there is still an orange peel effect, so it is flatted off with various grades of sandpaper before being polished back up to the final product which is amazing. Again quality control is such that the slightest mark showing and the piece is rejected
8 miles of wire goes into each car and the looms are so thick that they have to be heated in the oven before being flexible enough to be fitted on the car
We saw the powertrains being uplifted into the body shells which seems to be the only part of the factory where there is a automated production line
When you get to the end of the tour and pass through the finished cars some convertibles, lots of different colours, different bespoke interiors, they are truly amazing
We also saw Duncan who quite rightly is very proud to be part of the Bentley experience, and we all went for a very pleasant pub lunch.
I have probably forgotten some of what we saw, so maybe the others will chip in, but all in all a great day !
Robs Car Gallery
click below to access nano website
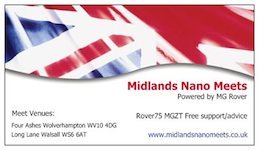
Planning is an unnatural process, much better to just get on with things, that way failure comes as a complete surprise instead of being preceeded by a period of worry and doubt